VERSIONE STAMPABILE (PRINTABLE EDITION)
MANUALE PRATICO DI REGOLAZIONE AUTOMATICA
(PRACTICAL HAND-BOOK OF AUTOMATIC CONTROL)
WORK IN PROGRESS - SI PREGA DI LEGGERE LA VERSIONE STAMPABILE
1. GENERALITA’
Il controllo di una grandezza variabile, generalmente funzione del tempo, nei processi e nelle lavorazioni industriali rappresenta un importante (e non facile) compito progettuale.
Spesso lo scopo del controllo è di mantenere costante il valore della variabile in questione, ma si può anche dare il caso che le variazioni debbano seguire un particolare programma orario.
In questa memoria ci proponiamo di illustrare quell’insieme di accorgimenti e di regole d’uso pratico da applicare sul campo, acquisiti in cinquant’anni di professione nella progettazione di macchine ed impianti.
Alcune definizioni:
• Variabile controllata: la grandezza sotto controllo (temperatura, pressione, portata di fluido etc.);
• Variabile misurata: il valore della medesima grandezza che sensibilizza la sonda associata al regolatore;
• Variabile manipolata: il valore della grandezza dopo l’insieme delle operazioni di correzione;
• Set point: valore desiderato nel processo per la variabile controllata;
• Disturbo: qualunque causa che provochi un’alterazione della variabile controllata;
• Errore: differenza tra il set point e la variabile misurata;
• Attuatori: dispositivi in grado di utilizzare i segnali di comando per pilotare gli elementi di controllo;
• Elementi di controllo: i componenti in grado di effettuare l’insieme delle trasformazioni (apporti energetici, scambi di massa, miscelazione di fluidi a diversa temperatura, filtrazioni etc.) atte a mantenere il valore di set point desiderato (valore di consegna).
Si distinguono diversi tipi di regolazione:
• Elettrica;
• Elettronica;
• Pneumatica;
• Autoazionata.
Per le prime tre la terminologia è ovvia mentre la quarta indica quei sistemi di regolazione che non necessitano di un’alimentazione dedicata (elettrica o pneumatica) per funzionare (come le valvole a bulbo e capillare dove la dilatazione di una sostanza fornisce l’energia necessaria a posizionare un otturatore, oppure come le valvole pressostatiche usate nella tecnica del freddo che prelevano una pressione al processo in grado di contrastare l’azione di una molla antagonista solidale ad un otturatore o allo stelo di uno stantuffo).
Si distinguono, inoltre, due grandi classi di regolazione:
• Ad anello aperto;
• Ad anello chiuso.
2. REGOLAZIONI AD ANELLO APERTO E AD ANELLO CHIUSO
Quando gli attuatori sono pilotati in modo indipendente dall’andamento del processo, ovvero obbediscono ad un segnale programmato non influenzato da una misura sullo stato della variabile controllata, la regolazione si dice ad anello aperto. Gli esempi tipici sono osservati nella famiglia degli elettrodomestici: la lavatrice, la lavastoviglie, il forno a microonde etc.
Un diagramma di flusso di questa classe di regolazione è rappresentato in Figura 1:
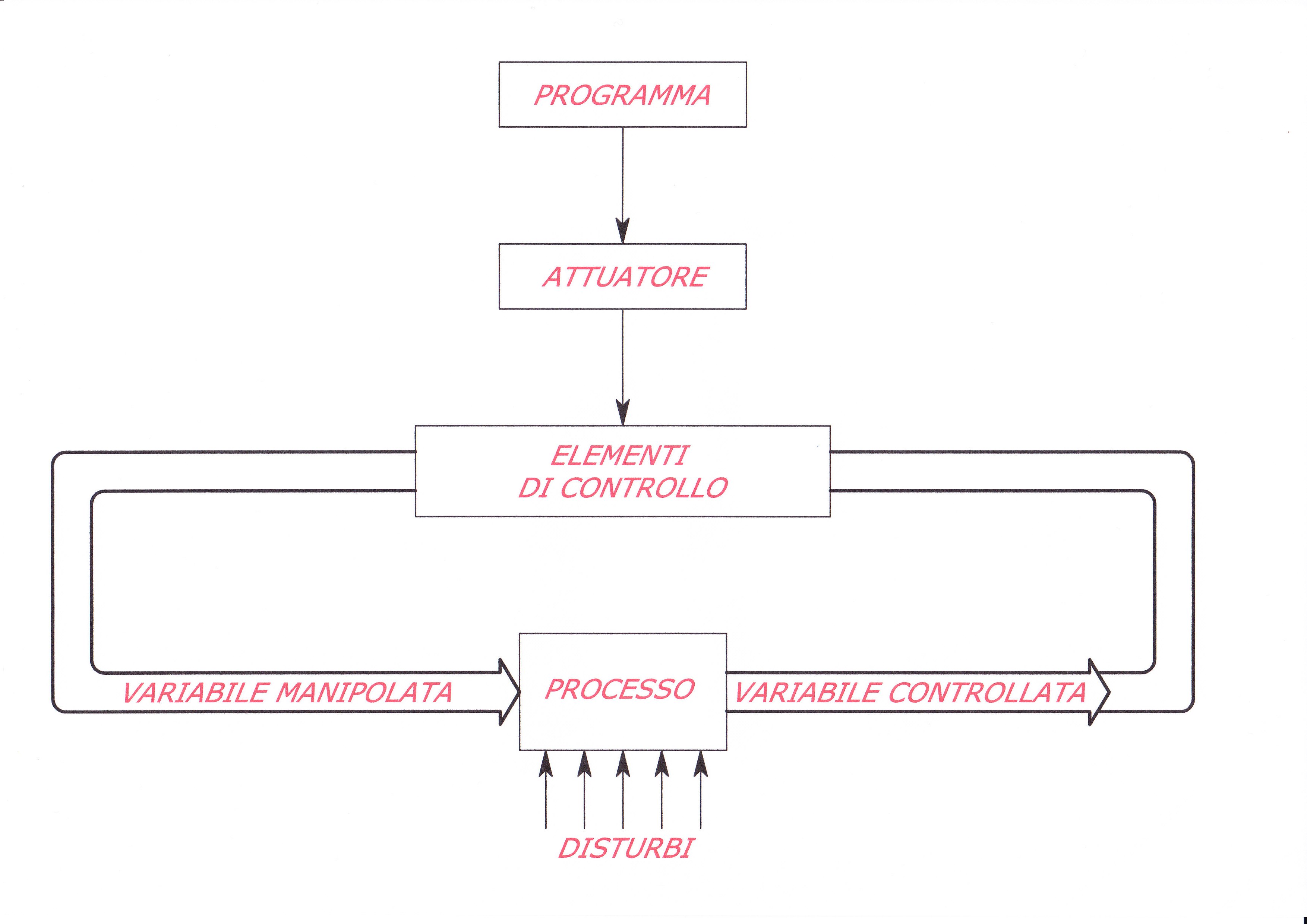
Figura 1 - Regolazione ad anello aperto (open loop)
Quando gli attuatori sono pilotati da un segnale contenente informazioni sullo stato del processo la regolazione si dice ad anello chiuso; il diagramma di flusso è rappresentato nella Figura 2:
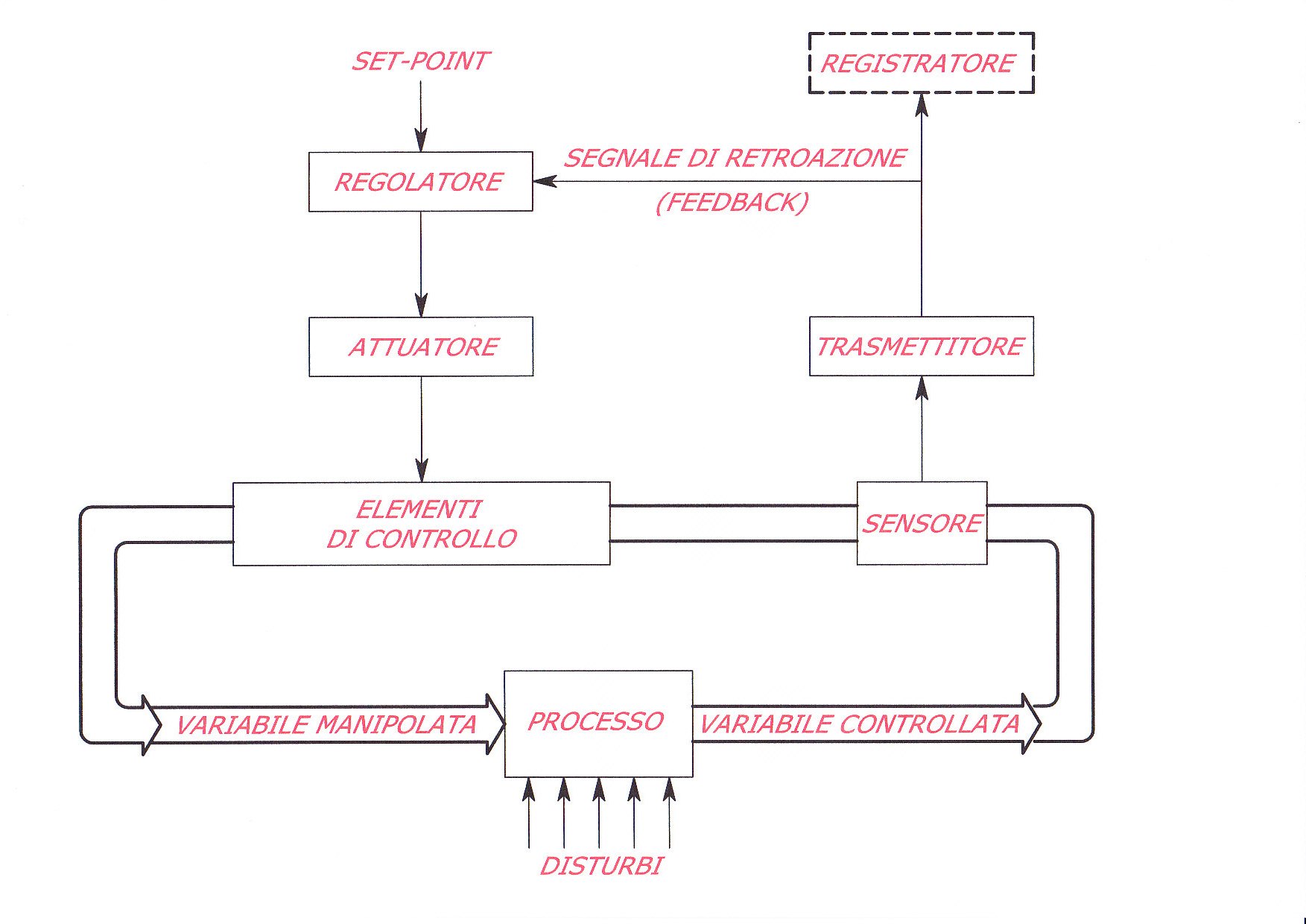
Figura 2 - Regolazione ad anello chiuso (closed loop)
Si suole anche dire che la regolazione ad anello chiuso è caratterizzata dall’avere un segnale di retroazione (feedback).
Le regolazioni ad anello chiuso possono essere di due tipi:
• On/off (o a due posizioni): come nel classico caso di un semplice termostato a bimetallo;
• Modulante: quando il regolatore che controlla il processo produce un segnale correttivo variabile in un intervallo prefissato (ad esempio 0./.10 V DC per la regolazione elettronica, oppure 3./.15 psi per la regolazione pneumatica) e, quindi, può posizionare gli attuatori in qualunque stato intermedio della loro corsa.
La figura seguente illustra, in modo sintetico, quel che si potrebbe dire sulla regolazione on/off:
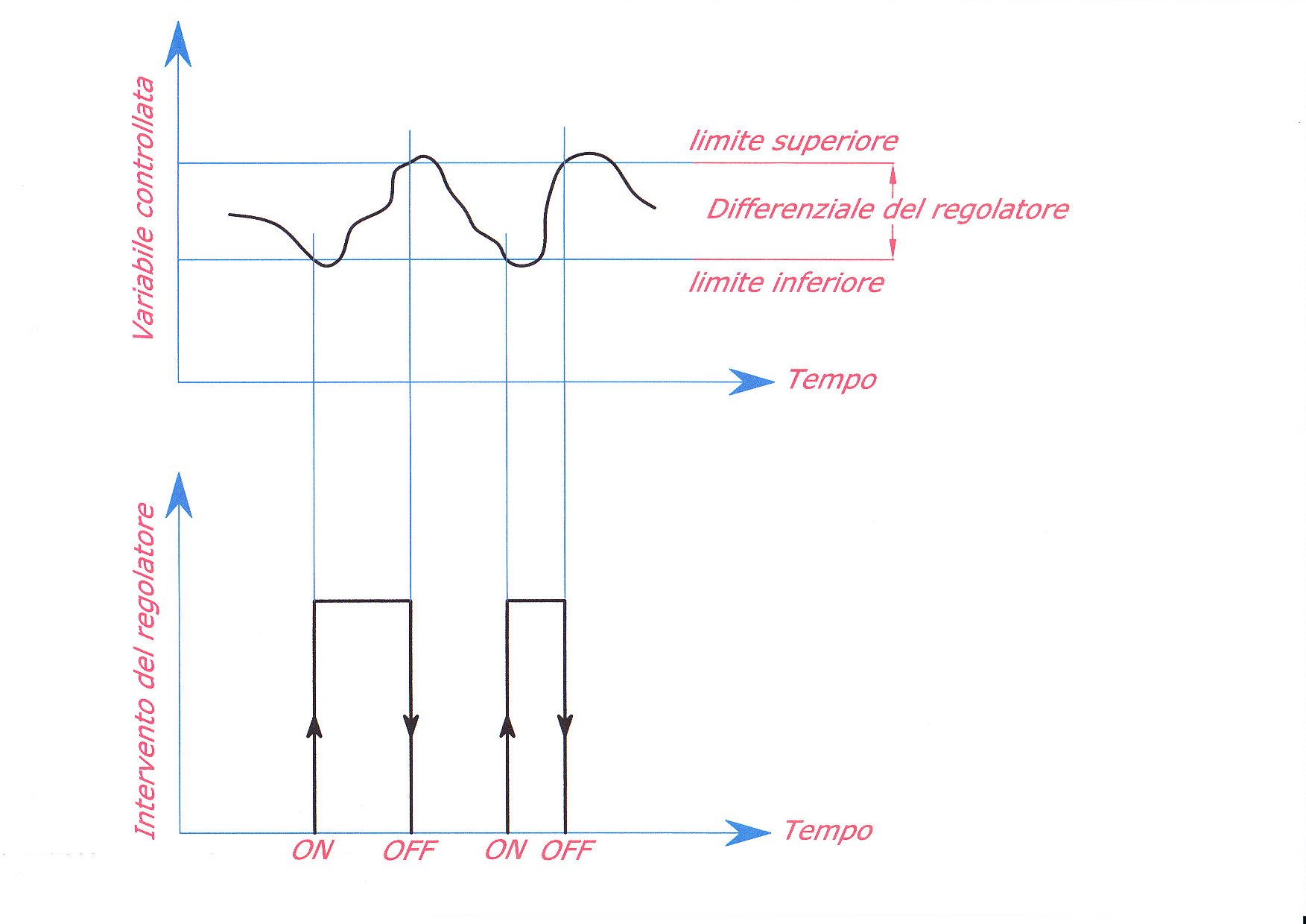
Figura 3– Le oscillazioni della variabile controllata sono comprese entro i due limiti, superiore ed inferiore (a meno di fenomeni d’inerzia termica), dipendenti dal differenziale del regolatore. Tale differenziale non sempre è regolabile. Lo stesso regolatore può essere dotato di diversi gradini
La regolazione modulante si basa sul segnale prodotto da un “nodo sommatore” in grado di confrontare il valore di set point con il valore della variabile misurata e di produrre un segnale proporzionale all’errore: il nodo sommatore che ci pare più esemplare è costituito dal Ponte di Weathstone.
Con riferimento alla Figura 4 ricordiamo che, quando tra le quattro resistenze costituenti i lati del ponte esiste la relazione
R1 : R2 = R3 : R4 ,
la differenza di potenziale elettrico tra i punti A e B è nulla.
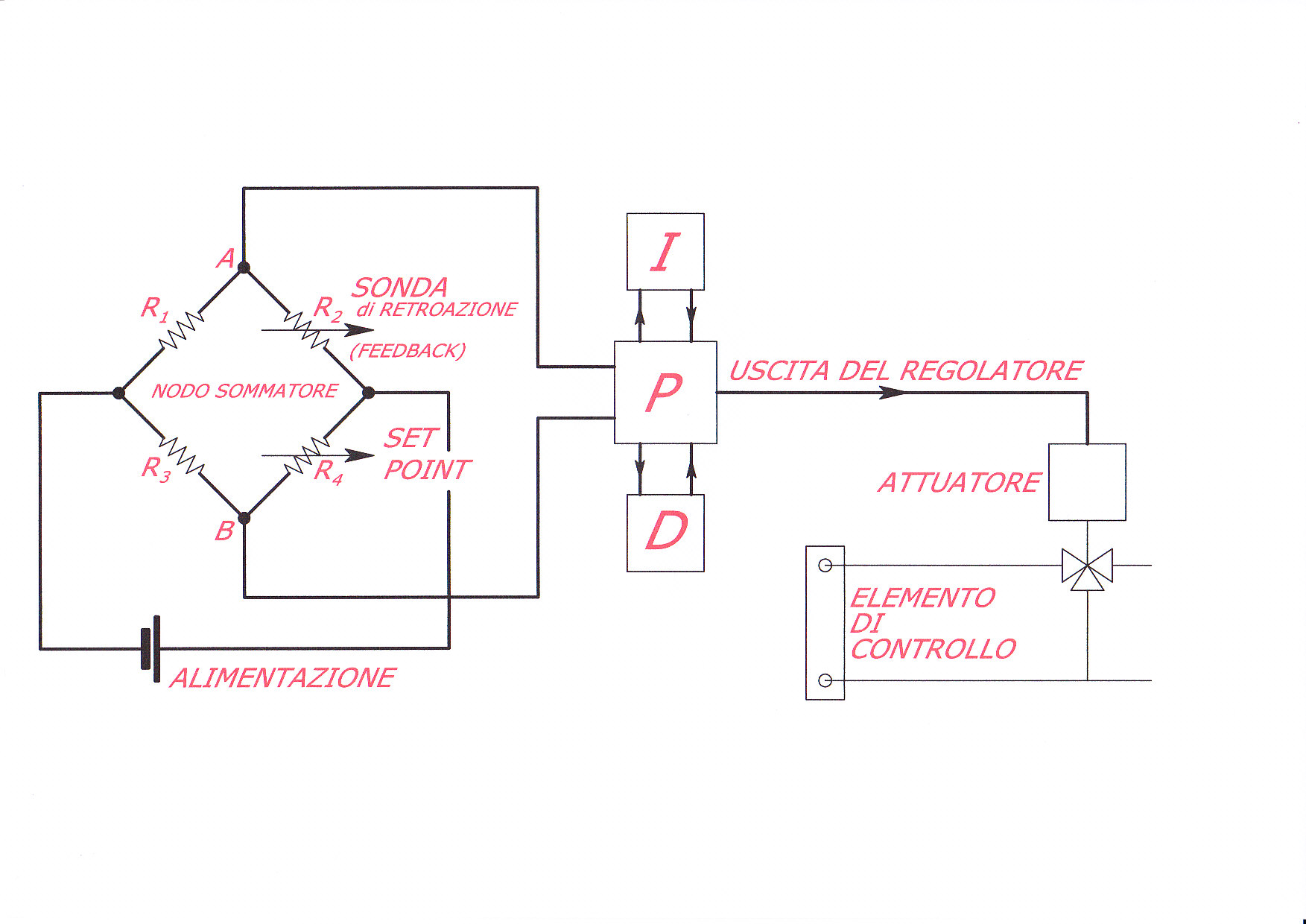
Figura 4 - Loop di regolazione con nodo sommatore a Ponte di Weathstone
Il sistema è fatto in modo che ciò si verifichi quando la variabile misurata (in questo caso rappresentata da uno stato di R2 ) ha il medesimo valore del set point (R4): in questo caso il segnale in entrata ed in uscita dal regolatore P è nullo (per il momento ignoriamo la presenza dei componenti I e D).
Se R2 ed R4 sono soggette a qualche variazione, un loro disequilibrio corrisponderà ad una situazione d’errore (già definito come scostamento tra set point e varabile misurata) che produrrà una differenza di potenziale “proporzionale” (anche se non perfettamente lineare) manipolata opportunamente dal regolatore P.
Il segnale prodotto da P sarà in grado di agire sull’attuatore che, tramite gli elementi di controllo, manipoleranno la variabile nel senso di correggere l’errore (senso che potrebbe essere, come vedremo, diretto od inverso).
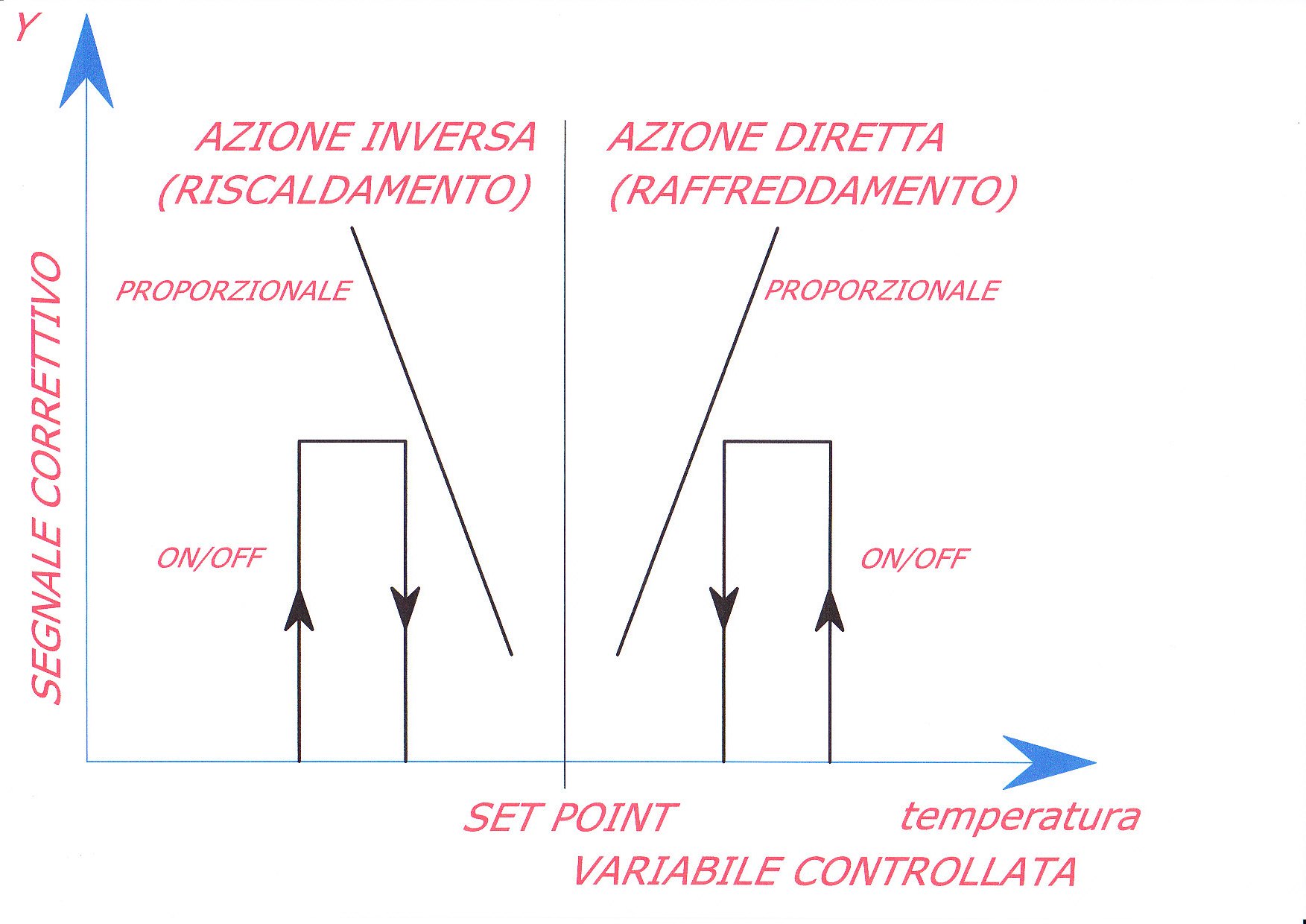
Figura 5- Schema tipico di una sequenza di regolazione (applicabile ad un trattamento aria): azione diretta ed inversa nel caso on/off e modulante
Nella Figura 6 si sono evidenziati i seguenti parametri:
• Banda proporzionale: è l’ampiezza dell’intervallo necessario alla variabile indipendente (X) affinché il segnale correttivo (Y) effettui una escursione completa del proprio campo (ovviamente distingiamo la B.P. diretta da quella inversa);
• Differenziale: è l’ampiezza dell’intervallo necessario alla variabile indipendente affinché il regolatore cambi posizione (anche qui distinguiamo un segnale on/off diretto ed uno inverso);
• A.I.: azione inversa (ingl. Reverse Action);
• A.D.: azione diretta (ingl.: Direct Action);
• Zona morta (ingl.: Dead Zone): è l’intervallo della variabile indipendente all’interno del quale non vi è alcuna azione correttiva né proporzionale né on/off.
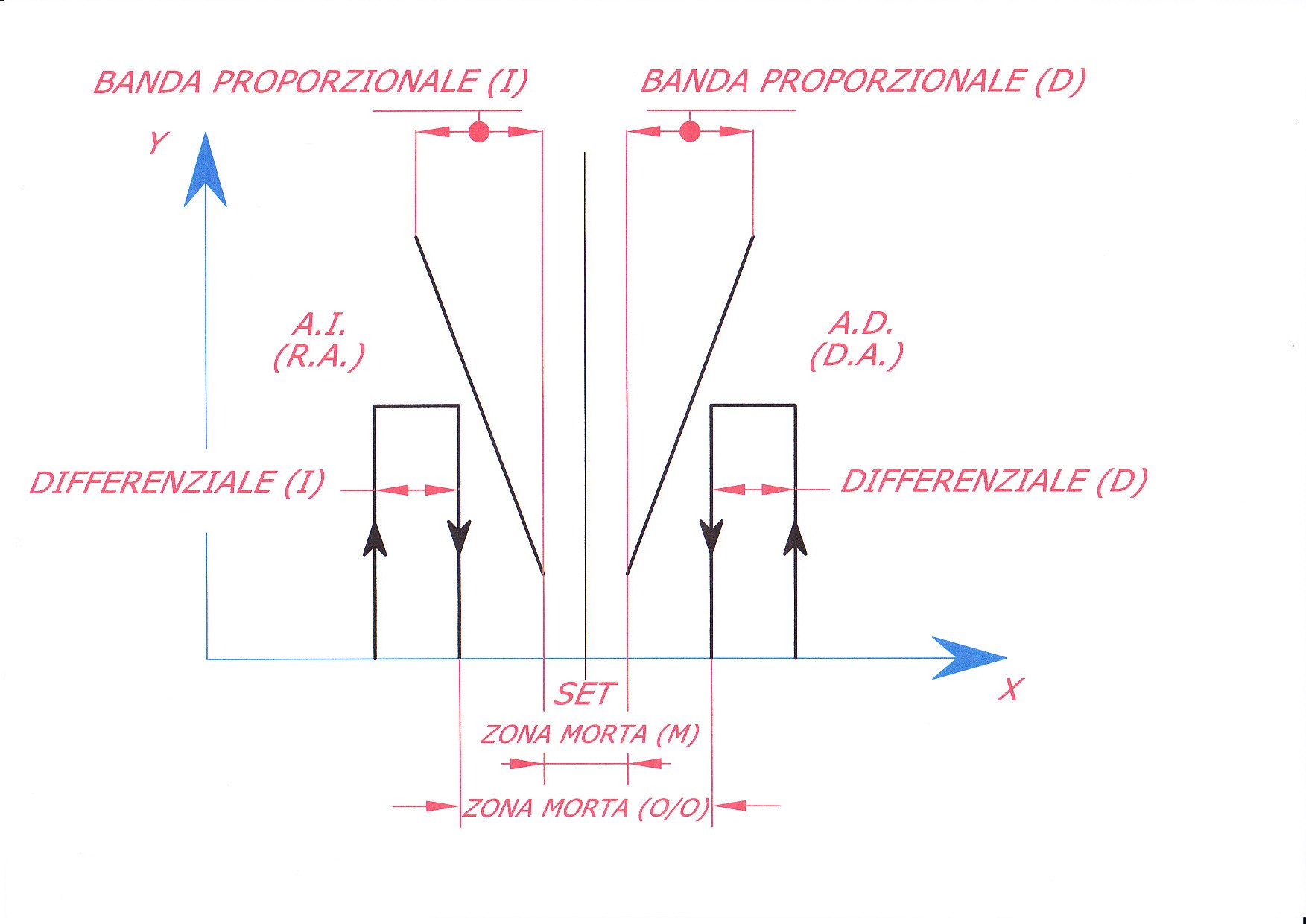
Figura 6 - Nomenclatura corrente applicata ai diagrammi descrittivi delle sequenze di regolazione. In tali diagrammi si rappresentano solo i segnali proporzionali (oltre agli on/off)
3. IL PROBLEMA DELL’OFF-SET ED I SEGNALI ADDITIVI
Osserviamo che la presenza di una zona morta è necessaria per evitare pendolazioni nel sistema, tuttavia, anche azzerandola, è ovvio che, per avere un segnale correttivo, è necessario che la variabile misurata sia fuori dal set (off-set).
Questo è un difetto insanabile della regolazione semplicemente proporzionale: se, per mantenere il valore di consegna (set point), è necessaria una posizione intermedia dell’attuatore, con il solo segnale proporzionale ciò è impossibile!
Si è escogitato, quindi, di sommare al segnale proporzionale (comunque essenziale) altri segnali “addizionali” in grado di permanere sull’attuatore anche al cessare del segnale proporzionale per raggiunto set point.
Questi segnali ausiliari, che permettono di risolvere il problema dell’off-set, sono di due tipi:
• Integrali: proporzionali all’area sottesa dall’errore (Figura 7 A);
• Derivativi: proporzionali all’inclinazione della tangente alla curva dell’errore (Figura 7 B).
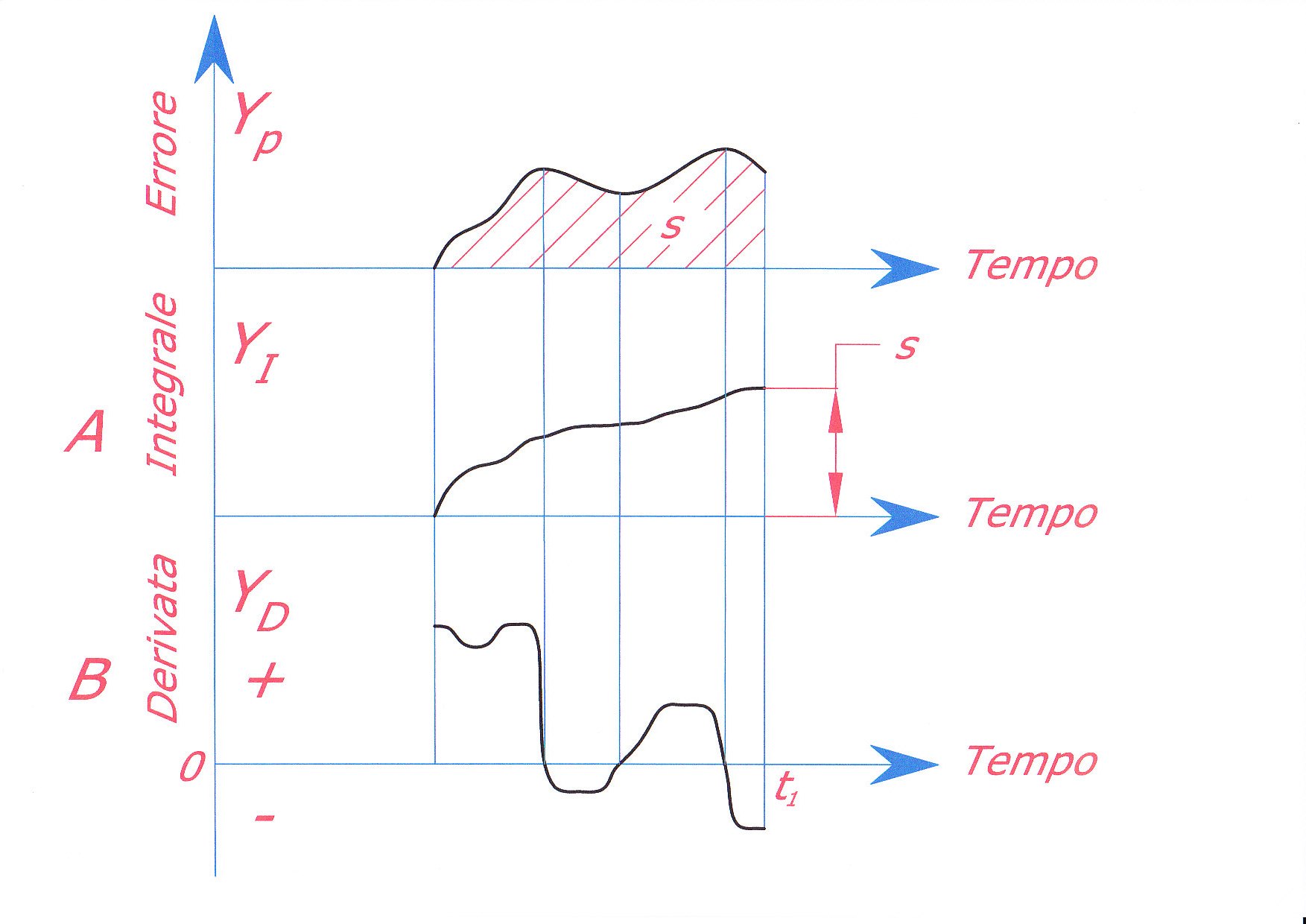
Figura 7 - Costruzione dei segnali additivi integrali e derivativi con riferimento ad una data curva d’errore
A seconda di quale segnale ausiliario si adotti, sono possibili tre combinazioni:
• P+I: proporzionale più integrale;
• P+D: proporzionale più derivativo;
• P+I+D: proporzionale più integrale, più derivativo.
Per capire bene il meccanismo applichiamo quanto detto a due tipi particolari di errori, a gradino ed a rampa, con l’aiuto della Figura 8:
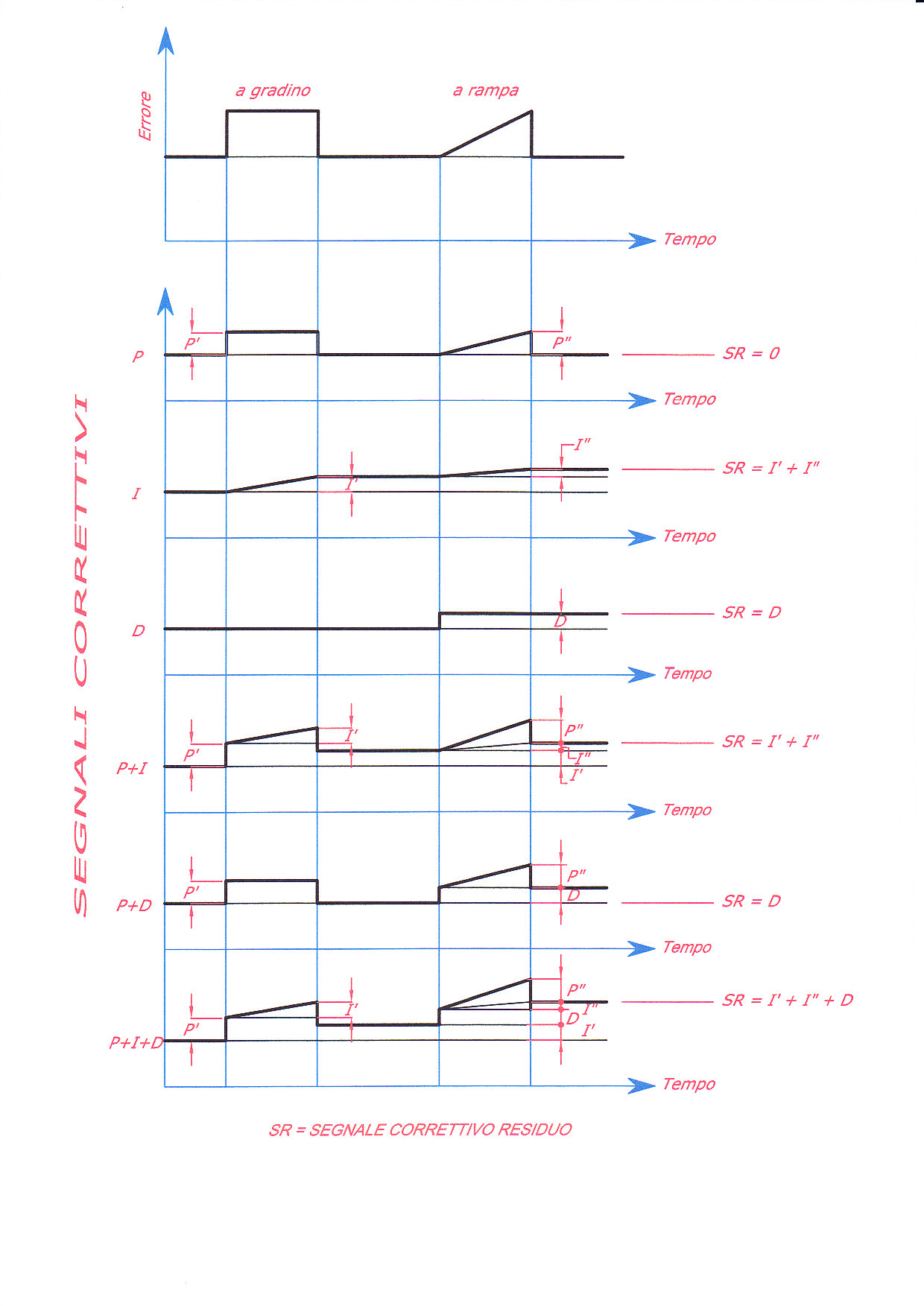
Figura 8 - Segnali P, I, D e loro combinazioni; solo i segnali additivi restano attivi anche ad errore nullo
• Errore a gradino: il segnale integrale è proporzionale all’area descritta dall’errore e la componente derivativa è nulla (perché derivata di una costante);
• Errore a rampa: il segnale integrale è ancora proporzionale come sopra, mentre la componente derivativa è costante (perché è costante l’inclinazione della funzione).
Se il segnale correttivo è puramente proporzionale una volta annullato l’errore esso pure si annulla. E’ presumibile che, nel caso più generale, ci sia ancora la necessità di una correzione ma, come già osservato, ciò richiederebbe uno scostamento dal set point: in pratica con una simile regolazione si realizza un regime persistente di pendolazioni che si può correggere solo a scapito della precisione.
Sarà, infatti, necessario allargare molto la banda proporzionale (manovra equivalente alla desensibilizzazione del sistema) finchè la misura della variabile oscillerà con frequenza ed ampiezza accettabili intorno al set point.
Se si dispone di un segnale additivo di natura integrale il segnale residuo sarà dato dalla somma I’ + I” il che ci permette di raggiungere lo scopo.
Nel caso che il segnale additivo sia solo di natura derivativa si avrà ancora un segnale residuo D’: limitato, però, al segnale a rampa poichè la derivata di una costante è nulla (il segnale a gradino è costante per ipotesi) ma, comunque, può essere efficace al raggiungimento dello scopo. Come vedremo meglio in seguito questo segnale ha l’importante proprietà di anticipare gli altri segnali.
Inoltre, come vedremo in Figura 9, esso può fungere da smorzatore alla correzione soprattutto in presenza di brusche variazioni della variabile controllata.
Quindi nel caso P + I il residuo sarà I’ + I” e nel caso P + D il residuo sarà D’ mentre nel terzo caso, P + I + D il residuo sarà la somma dei precedenti residui: I’ +I” + D’; gli ulteriori scostamenti della variabile misurata rispetto al set point provocheranno variazioni nei segnali residui secondo il meccanismo esposto(1).
Dalla Figura 8 si evince che il solo segnale PD non assicura sempre la soluzione del problema dell’off-set, infatti in un errore a gradino non si ha alcuna azione derivativa.
In sintesi si può dire che il regolatore PID produce un segnale correttivo dipendente da:
• Scostamento della variabile dal set point (azione P);
• Durata dello scostamento (azione I);
• Velocità di variazione dello scostamento (azione D).
Se il sistema di regolazione viene opportunamente “accordato” al processo (nel modo che vedremo), con la combinazione PID si può ottenere una regolazione tecnicamente perfetta.
4. QUANDO L’ERRORE CAMBIA SEGNO: LA REGOLAZIONE IN SEQUENZA
Per fissare le idee supponiamo di voler regolare la temperatura di un ambiente condizionato con carichi interni variabili (quindi non la regolazione con commutazione stagionale in cui d’estate solo si raffresca e d’inverno solo si riscalda); ci possono essere dei momenti in cui la temperatura (variabile misurata) è sopra il set (quindi con errore positivo) ed altri in cui è sotto (errore negativo).
Adattando la Figura 7 avremo la rappresentazione di Figura 9 .
Il cambiamento di segno nell’errore fa in modo che anche l’azione correttiva proporzionale cambi di segno; ad esempio sarà necessario passare da un riscaldamento ad un raffrescamento della variabile manipolata. Il regolatore dovrà, pertanto, produrre due distinti segnali in uscita, ad azione contrapposta, in modo da pilotare degli attuatori distinti ed associati ad elementi di controllo con opposti effetti termici; proprio come mostrato nella Figura 5.
Figura 9 - Andamento delle uscite quando l’errore cambia segno; notare che il segnale derivativo, oltre ad “anticipare” P e I, tende ad aumentare quando aumenta l’errore (in senso assoluto), mentre diminuisce quando questo tende a diminuire
Il regolatore, in base al verso della corrente generata dalla differenza di potenziale VA-VB (Figura 10), indirizza il segnale su un’uscita (ad esempio ad azione diretta) o sull’altra (azione inversa)(2).
Nella Figura 9 si può, anche, notare l’effetto di anticipo del segnale derivativo: essendo proporzionale alla tangente della funzione P esso assume subito un valore diverso da zero anticipando tutti gli altri segnali.
Figura 10 - Il nodo sommatore deve tenere conto del cambiamento di segno dell’errore in modo da produrre un segnale con senso d’azione adeguato (v. anche la figura precedente)
Con i regolatori elettronici esistenti oggi sul mercato si possono realizzare le sequenze più disparate. Chi scrive ha vissuto dal di dentro tutta l’evoluzione dall’elettrico all’elettronico: i regolatori programmabili (croce e delizia degli installatori!) consentono di optare per molteplici segnali modulanti ed on/off con il medesimo strumento e con dei costi di hardware sempre più abbordabili.
Dal nostro archivio abbiamo tratto la Figura 11 che si riferisce ad una regolazione, tutt’ora funzionante (Istituto Europeo di Design – Milano), avente, come elementi di controllo, una batteria ad acqua calda (con limite di minima), un sistema di termostrisce radianti a soffitto, due gruppi ad espansione diretta con inserzione binaria (v. “Espansione diretta: ritorno al futuro”) e la possibilità di free-cooling “termico” (in antitesi ad “entalpico”).
Una regolazione accurata è condizione necessaria per evitare gli sprechi energetici; infatti risparmi anche percentualmente modesti quando sono applicati su 7./.8000 h/anno danno risultati più che apprezzabili; se si calcola il ROI (tempo di ritorno dell’investimento) di una buona regolazione (che può costare solo qualche unità percentuale dell’impianto) il recupero economico può avvenire in una sola stagione!
Figura 11 -- Una volta definiti gli elementi di controllo si programma, con un grafico di questo tipo, la successione delle sequenze di regolazione: lo strumentista programmerà il loop di regolazione e provvederà all’accordatura della regolazione stessa con l’impianto, in sede di collaudo, fino ad ottenere il funzionamento desiderato
5. REGOLAZIONE MODULANTE: CONTINUA, A TRE PUNTI E FLOTTANTE
La regolazione modulante può essere di tre tipi:
• Continua
• A tre punti.
• Flottante
La regolazione con segnale continuo (come fin qui descritto) è tipica dei sistemi elettronici e pneumatici, mentre nella regolazione elettrica è inevitabile il ricorso ai tre punti (ma anche nei sistemi elettronici si può adottare tale tipo potendosi utilizzare come attuatori dei motori in corrente alternata).
Un dispositivo (per la verità piuttosto arcaico) prevede che l’elemento sensibile alla grandezza misurata agisca sullo spostamento di un cursore associato a due avvolgimenti (a guisa di doppio potenziometro) come nella Figura 12.
Figura 12 - Schema di una trasduzione “elettrica” a tre punti (A = rotazione oraria, B = zona morta, C = rotazione antioraria)
Nel caso che il cursore+doppio potenziometro venisse sostituito da un contatto di scambio del tipo 1/0/2 l’attuatore tenderà a fermarsi solo a fine corsa o a mezza via se l’azione correttiva viene a cessare. Questo è il principio della regolazione flottante sui cui limiti ci sembra superfluo discutere.
Grazie all’elettronica il meccanismo cursore+doppio potenziometro viene sostituito da componenti allo stato solido, cosicché il sistema diventa assai più affidabile ed il montaggio si effettua con dei collegamenti a morsettiera come indicato nella figura seguente:
Figura 13 - L’elettronica consente di sostituire componenti meccanici soggetti a manutenzione e ad usura con componenti allo stato solido
La regolazione a tre punti,va considerata modulante anche se discontinua e, se il regolatore è adatto, può esercitare le funzioni PID con risultati pratici paragonabili alla continua.
6. UNA REGOLAZIONE DI MASSIMA PRONTEZZA E PRECISIONE: MASTER/SLAVE
Chiameremo “ciclo” (loop) l’insieme delle operazioni che compongono la seguente successione:
1) rilievo della misura da parte del trasmettitore,
2) suo confronto con il set,
3) determinazione dell’errore,
4) produzione del segnale correttivo,
5) intervento degli attuatori,
6) azione degli elementi di controllo,
7) modifica della variabile manipolata,
8) azzeramento dell’errore (ovvero raggiungimento del set-point).
Per fissare le idee applichiamo le seguenti osservazioni al caso di un condizionamento dell’aria: poiché è necessario che la misura della variabile venga rilevata con una sonda all’uscita dal processoƒv3), il tempo necessario all’azione correttiva potrebbe richiedere particolari portate d’aria in modo da abbreviare il periodo del ciclo rendendo più pronta la risposta del sistema regolatore.
Con riferimento al volume del locale trattato si hanno, in pratica, le seguenti portate in circolo:
• Ambienti residenziali in climi temperati: 5./.7 vol/h,
• Idem in climi torridi: 10./.13 vol/h,
• Camere bianche: 50./.100 vol/h.
Nel primo caso il tempo minimo per realizzare un ciclo è di circa dieci minuti primi; nel secondo è di cinque e così via, ma non è detto che un ciclo sia sufficiente per raggiungere le condizioni di set: potrebbero essere necessari tre, quattro o più cicli.
Tale tempo potrebbe essere eccessivo per il tipo di destinazione d’uso cui è dedicato l’ambiente condizionato (pensiamo, ad esempio, ad un reparto di confezionamento di specialità medicinali). Al fine di ottenere tempi di loop molto più brevi si può ricorrere allo schema seguente:
Figura 14 - In questo schema si hanno due regolatori: il master è sensibilizzato dalle condizioni di ripresa e la sua uscita viene utilizzata come set-point (variabile) per il regolatore slave sensibilizzato dalle condizioni di mandata.
Il regolatore master, tramite il relativo sensore, raccoglie le informazioni sull’andamento del processo, d’accordo con quanto evidenziato nella nota precedente (le condizioni all’uscita rappresentano, comunque, il valore nominale della grandezza controllata).
Tale misura viene confrontata, col set point desiderato dal processo nel regolatore master, il cui segnale correttivo non agisce sull’attuatore, ma modifica il set point del secondo regolatore (slave) che è sensibilizzato dalle condizioni di mandata. Ne risulta che gli elementi di controllo agiscono in base alle condizioni di mandata, con tempi di reazione immediati, ma in modo tale da soddisfare il regolatore primario, il master, sensibilizzato dalle condizioni di ripresa.
Figura 15 - Sopra è rappresentato un regolatore master, con registratore(4), in grado di controllare e registrare due variabili. Sotto i regolatori slave, relativi al master detto, che pilotano gli attuatori sulla mandata
7. L’ACCORDATURA (SINTONIZZAZIONE) DELLA REGOLAZIONE ALL’IMPIANTO
Un anello di regolazione funzionante a regola d’arte deve essere in grado di offrire le seguenti caratteristiche:
• Sensibilità: dipendente, in primis, dalla larghezza della banda proporzionale;
• Prontezza: funzione delle inerzie temporali che caratterizzano i vari rami dell’anello;
• Precisione: dipendente dall’efficacia dei segnali addizionali.
Per regolare la larghezza della banda proporzionale (BP) ricordiamo che essa può essere definita in due modi:
• In termini percentuali: data l’ampiezza di un campo di lavoro (span) caratteristico dello strumento, p.es. 40 °C, una larghezza di banda del 10% corrisponde a 4 °C; ciò significa che con una variazione di 4 °C della variabile regolata il segnale proporzionale varia tra il minimo ed il massimo;
• In termini assoluti: la scala della banda proporzionale può essere tarata direttamente in unità della grandezza controllata (p.es °C).
Per quanto riguarda l’intensità del segnale integrale (integral action time o RESET) essa dipende da una scala che può essere definita in due modi:
• Ripetizioni per minuto (rip/min, ovvero frequenza): istante per istante il segnale integrale aumenta con una velocità tale da ripetere il segnale proporzionale un certo numero di volte ogni minuto primo(5);
• Minuti per una ripetizione (min/rip, ovvero tempo d’integrazione): ovviamente è la scala reciproca della precedente e può essere definito come il tempo necessario (in minuti primi) perché l’uscita vari da zero al proprio massimo con un errore fisso pari alla banda proporzionale.
________________________________________
(5) Poniamo di avere un segnale proporzionale all’errore Y, come mostrato nella figura acclusa. Per fissare le idee abbiamo impostato un tempo di ripetizione pari ad un minuto, abbiamo, anche, supposto un segnale P a gradino, per semplicità. Ad ogni minuto il segnale Y viene ripetuto di modo che dopo 2,5 min’ il segnale raggiunga il valore di 2,5 volte il segnale P, che rimane nell’attuatore come segnale residuo al cessare di P, per raggiunto set point. Se P fosse variabile con continuità si tratta d’immaginare tanti gradini in successione di larghezza sufficientemente piccola
Anche la scala del segnale derivativo (derivative action time o RATE) può essere espressa in due modi mutuamente reciproci:
• Tempo di derivata: esso è definito come il tempo necessario al segnale P per raggiungere da zero il valor massimo con errore a rampa(6).
• Frequenza derivativa: è la scala reciproca della precedente.
Una volta che l’insieme degli organi di controllo (valvole a tre vie, serrande, umidificatori, pressostati, ventilatori etc.) hanno i sensi d’azione previsti, sono tarati sul set point di progetto etc., esaurite le verifiche preliminari, anche di natura meccanica, ritenute opportune, si avvia l’impianto facendo il “set up” della regolazione che a noi, patiti della musica, piace chiamare “accordatura” (nel linguaggio tecnico, assai più prosaico, si parla di “sintonizzazione”…).
Procedura consigliata per l’accordatura:
1. Si minimizzano gli effetti dei segnali addizionali rendendo minimo il tempo derivativo e massimo quello integrale;
2. Si imposta una banda proporzionale ampia (p.es.: 100%);
3. Si porta in “leggera” pendolazione persistente la variabile controllata restringendo la BP;
4. Si aumenta l’azione derivativa finché la pendolazione scompare;
5. Si ripetono le operazioni 3. e 4. finché un ulteriore aumento dell’azione derivativa non riesce ad eliminare la pendolazione;
6. Si aumenta l’azione integrale fino a che la variabile presenta l’andamento desiderato. Secondo le osservazioni degli addetti ai lavori i tempi integrali potrebbero coincidere con quelli derivativi.
(6)
Dato un segnale proporzionale YP a rampa costante il segnale derivativo YD tenderebbe a posizionarsi al valore Y che compete alla pendenza della rampa. Il tempo necessario a YP per raggiungere YMAX, partendo da zero, costituisce il “tempo di derivata”. L’operatore può scegliere l’ampiezza del segnale derivativo da avviare all’attuatore agendo sulla scala 0./.100% del tempo di derivata. Nella figura si è scelto il valore del 25% ed segnale D si è fermato a Y25%. Si ricordi che il valore della tangente (trigonometrica) della rampa è immediatamente individuata dal regolatore: è per questo che YD ha, come già osservato, anche un’azione anticipatrice sugli altri segnali
Si potrebbe, prima di concludere, osservare che si può fare ancora una distinzione tra i regolatori:
• Regolatori a zero vivo: quando il segnale proporzionale in uscita è maggiore di zero anche a set point raggiunto (p. es.: 2 psi nella regolazione pneumatica, con gli attuatori tarati a 3 psi) il vantaggio è dato dal fatto che lo strumentista sa che un eventuale segnale nullo corrisponde ad una mancanza di alimentazione;
• Regolatori a zero morto: in caso di uscita nulla lo strumentista potrebbe avere il dubbio se ciò fosse dovuto al raggiungimento del set point oppure ad una mancanza di alimentazione.
Concluse le operazioni di set up si può procedere al collaudo (start up): la sequenza operativa sopra descritta ha la sola pretesa di essere orientativa e richiede anche quella classica “malizia” che l’esperienza insegna. E’ necessario essere osservatori pazienti ed accurati: si avrà la professionale soddisfazione di un’opera compiuta con tecnica si, ma anche con arte.
Si ricordi, inoltre, che in tutti i grafici che abbiamo riportato, la trasmissione dei segnali è presunta come immediata: in realtà ovvii fenomeni inerziali rendono i gradini, le rampe e tutti i segnali in genere più curvilinei.
E adesso… al lavoro!...
piermariaboria@alice.it
E' DISPONIBILE LA VERSIONE STAMPABILE